There are many opinions on the best way to achieve a Safe work place through the purchase of Industrial Safety Supply products that enhance your injury prevention process. I have an opinion too, and I know it's the right one. This article regarding purchasing Industrial Safety Supply products is within a series of articles about reducing on the job injuries and setting up an effective Industrial Safety Supply Purchasing Plan that works hand and hand with your overall Injury Prevention Process. Texas Safety Supply will have the Safety Supplies that you need to assist you to jettison your current results and make your work place a Better, safer place to work.
Lasting Changes to Reduce on the job injuries
Really, the only doorway to long term change and long term success is far different the injury prevention plan used by most Mid to Large size companies today. I suggest an approach to buying Industrial Safety Supply products through a more inclusive, extensive process that we apply through a David Cooperrider and originator of the Appreciative Inquiry approach to Problem solving. Mr Cooperider is a Professor at the prestigious Case Western Reserve University in Cleveland Ohio. The Appreciative Inquiry approach to problem solving and Corporate Change Is a method that I believe will help you achieve long lasting results and a long lasting change in the culture of your workplace. It's not a quick Fix approach, but it is an approach that can and will bring rapid improvement that continues on a positive trajectory. My experience is that it does not level off. It works towards a Zero defect ultimatum where all employees of a company are "actively engaged" in achieving world class results. More about David's approach to Problem solving in a bit. Quickly, a review of how the process works in most Mid to large size companies today.
Purchasing Industrial Safety Supply Products
Selecting the right Industrial Safety Supply products for your facility and the preferred Safety Supplies can be a daunting decision in the work place. The age old question of balancing Cost and quality. How is this done by most companies and what is the decision process that is made in the purchase Industrial Safety Supply products ? Is the decision based upon cost alone? Well that's no good. Perhaps by the Look and feel of the industrial Safety Supply product while sitting in a Corporate office? Maybe. But that's not the answer either. Perhaps based solely on the input of a knowledgeable sales representative from a Safety Supply company. Better, But an Industrial Safety Supply rep is only part of the answer in an Injury prevention process. It's not the "End of the Line" as the Travelling Wilburys used to sing.
Old School Problem Solving
Typically in the Corporate world a CEO, President or other bigwig sees that a Poor safety record has caused a company's insurance rates to go up and is having a negative impact on investors in that company. Poor Injury Rates have a negative affect on bottom line of any company. Profits are down, costs are up. Hiring costs increase as additional people are hired to replace those the wounded. Training costs are up getting the 'newbies' up to speed. Additional dollars are thrown at purchasing additional Industrial Safety Supply products looking for the magic sauce to solve the problem. Productivity is down because the new guy and girl, well they are just not quite as efficient as the guy who is at home because he was seriously hurt on the job last month. So Costs are up, profits are down and now the President knows that he has to do something before the Board of Directors Meeting next month as she will surely be questioned about what they heck is going on within our Company? So what does she do? It's time for the Old "Action Plan".
Have had one of those at your company? A new program, a new process?
Industrial Safety Supply and Implementing change
Let's talk about the old way for implementing Change...stick with me a bit.
Typically, an important Leader within an organization decides that there is a need for a change within the organization. Something needs to be fixed. So what does he do. He calls together his underlings and direct reports and informs them that their is a need for a change and "dad gummit" it it better happen pretty quick and it better achieve the desired result. ( Probably leaves out the upcoming Board Meeting Part ) Let's use the company's Injury frequency as an area where an improvement plan is being put in place from "on high"
So, in the typical organization, a bunch of men and women with expensive clothes, shirts, ties and suits will sit around a room and come up with a plan about how to fix a problem that they don't have all the facts on about a job where injuries occur that they themselves have never done. Their plan is to fix the problem. I do not like the odds. Granted some of the things they identify are important, but they don't see everything, they don't know everything, they do not have all the facts. Forgive them, they don't know everything. They are not the ones doing the job where people actually are getting injured. Au contraire, mon amie. They are several layers removed. They're the analyst. It's what they do and what they do it well. They analyze facts, numbers, trends and come up with a well intention-ed solutions. But it's their solution, and their solution alone. Maybe even put the solution in a book, a folder, to make it look like it's important and give it the level of respect that they think this plan is worthy of. In most cases, very little input from anyone without that expensive suit.
The Old Cram Down Method of Implementing the new Safety Plan
Now it's time to disseminate the plan, so they send the plan down to Regional and Facility Managers and normally send along some "fear and threats" in the envelope as well. "Implement the plan they say." So these mid managers do some implementing. They are willing and able to implement the plan, they may not know why or what parts of it are for, but they'll do their job and implement the plan. But something happens. Parts of the plan are lost. Ever play the old game of "telephone" sitting around the kitchen table?. Details, why and what fors are lost in the messaging. But now the Mid Manager has done their part of the implementing the plan from "on high". Now it's get passed on in the game of telephone to the next layer.
Pass the Industrial Safety Plan to the Front Line
"Tag", now the shift supervisor or the shift manager is it. Now they are told why the Plan is important and must be implemented. In a hurry. So the shift supervisor, having lost some of the message again in the "telephone" chain of communication, explains the Plan to the front Line employee, he has them sign the Meeting Log to show they have heard about the Plan. And the front line employee goes off to do their job, pretty much the same as they did it yesterday. People want to excel at what they do, they want to be good at it, and they will try to change what they were asked to do, to work safer as the "Plan" asked them to do. But this kind of change, well it just does not last. People go back to what the corporate culture allows and permits. They go back to what the acceptable Culture is. A young lady working on the front line performing a job that requires hand protection with the use of cut resistant gloves to protect her hands from cuts and punctures from sharp objects, in need of the right Industrial Safety Supply Items, the Best Cut resistant Gloves. Well she may have heard the plan, but if the right industrial Safety Supply items are not available to allow her to do her job in a safe manner, how seriously is she going to believe in the "Plan". Probably not too much. There is no "buy in" from the people actually doing the job. There may be some short term improvement but this is driven by "fear". The "or else" mentality. Do it "or else". Get me my number "or else". We're all running from the same fear of loosing a job for fear of not achieving the results. But pretty sooooooon....the focus goes away. The new Focus is directed at another number. And hence, a "New plan" for something else that takes the attention away and directs it at something else.
Long Lasting Changes in Industrial Safety Supply and Injury Prevention
Let's talk about a relatively new method to Organizational Change, a solution to long lasting change and problem solving. One where the "culture' really does change. That is the David Cooperrider Appreciative Inquiry approach.
Quick Story; I became a believer in this approach to Injury prevention and Purchasing Industrial Safety Supply products approximately fifteen years ago. I worked at a truly leading edge organization in the Less Than Truckload Freight business as a Facility Manager that taught these Appreciative Inquiry approach to implementing change to Senior Managers as well as other selected managers and it became the way for 'doing business' in that company. Tough to imagine but true; old school LTL truck business with new wave change management. I ultimately left that company ( that's a different story ) and went to a company that had the Top Down approach down pat. Plans from on high, threats for results, the "Or else" mentality. Here we go.
When I arrived at my new position at a Freight Terminal, well we were "good" at injuries. We had 400 front line employees and we had over 350 injuries in one calendar year. Can you imagine that? An injury a day. But that was ok with all. It was acceptable. Corporate culture said it was ok. Guys driving forklifts off docks, playing bumper cars on the dock. Crazy. A culture that accepted work place injuries as just a cost of doing business. Guys and Girls get hurt, deal with it. Human Resources could not hire and train people fast enough to replace all the people getting hurt.
Two years later that same facility had 26 injuries for the year.
These results were achieved through an Appreciative Inquiry approach to Organizational Change fathered by David Cooperider with Case Western Reserve University in Northeast Ohio.
An Appreciate Inquiry Approach to Injury Prevention and Purchasing Industrial Safety Products
The Appreciative Inquiry approach to solving problems begins from the Bottom of an organaizational chart and Flows up. So, the absolute reverse top down approach to Most Mid to large size companies problem solving that goes on today. So those most affected by the change area or the Improvement Focus area of an organization, well they are the ones most directly involved in identifying the solutions and that change Begins with a positive affirmation about a Positive feeling or Result at the company and sharing it with others.
The Appreciative Inquiry approach to problem solving looks like this:
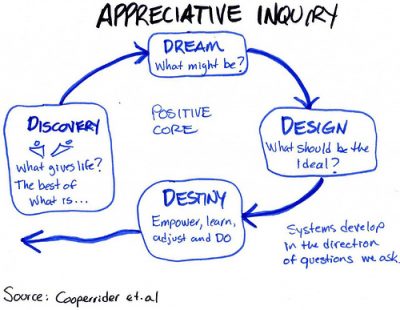
Discovery
The key difference with the "AI" approach to changing the culture begins with a "summit." Through involvement of all the "stakeholders" within that organization as much as possible or significant representatives from all parts of an organization. In solving injury issues, the key players are the front line employees that are more susceptible to injury. Frontline employees are the key players and thus the "Summit" group should be skewed in that manner. But in identifying Injury solutions, part of the equation is going to be Industrial Safety Supply. Do we have the correct safety supplies for employees. Therefore, Purchasing is a key player in the role that they play in purchasing Industrial Safety Products.
The process begins with A positive affirmation Process where employees interview each other; identifying when they felt most alive, most successful at work. When were they at their best. Why did that happen, what forces allowed you to be successful? All are equals in this search. Then all are encouraged to share. This develops commonality, we are in this together, we all want the same thing. For the company to be sucessful and to be able to go home very day safely to Loved ones.
Dream
Stakeholders then Dream of what is Possible in this Change area. It's not guys and girls alone speaking in a Conference room, and it's not front line employees alone in a Break room. All are mixed in discussing what is possible. Purchasing brings their expertise, front line employees their safe work expertise, Supervisors, Managers, Janitors, General Counsel. All are present to develop a comprehensive solution. Frontline employees can explain better how hand injuries happen. Purchasing may be able to purchase the right Industrial Safety Products at Higher levels of protection driving injury costs down, All are involved to dream Widely, to set the Bar high for the Collective desired result.
Design
Now the Solutions are developed, All are on the same team. No one questions why we stretch before work, their is a reason for it. It's not a plan from the Commissioner. We understand why we do what we do together. We are in this together. It is ok now for any employee to confront any employee for any unsafe act they may commit in the work place. Front line employees can confront a VP and it is thanked rather than rebuffed.
Destiny
Now make it a reality. Work towards a common purpose that all are involved in and understand the goal is success. The Goal is to achieve that Positive success that you have experienced at work in some other area. Transference and a Positive change in corporate culture will be the result.
Through this collectively, engaged process of changing Corporate Culture people will feel more connected to the place that they work. That their opinion matters. That the opinion of others matter. Front line people learn that their is a cost if they are off injured. Much more than just their paycheck. Replacement costs for hiring, training and efficiency drop offs. This ultimately makes their company less sustainable for the Long run and their may be no job to come back to when you are better. Senior level managers learn that the front line people have the same dreams, they want to do their job well. They want their knowledge and opinion to matter. In the case of Industrial Safety Supply and Injury prevention, all will work together on the common goal.
How often I have seen when the problem area is put "into the hands" of those that do the work and they are given trust, and are listened to, they will identify the solution. The right solution. The Long lasting solution. Front line people will hold each other accountable out of love and concern for their fellow employee. It's really cool to see this environment foster and take hold in the work place.
Employee Involvement in Selection Industrial Safety Supply Products
Top down plans, how ever well intention-ed, rarely result in Long Term culture change. Bottom up plans, with top level equal involvement,...well those plans work well. They send people home safe. They put the right Industrial Safety Product on the employee to keep them safe while performing they tasks that have potential for injury. The Bottom line cost for Industrial Safetyy Products actually go down because employees know that Management cares and buys them the Best Industrial Safety Products available so they can do their job well, and do it in a Safe manner.
So get people involved. If you want Long term results, then get the people that do they job involved in the "fix". Get them involved in the Injury Prevention process and selecting the right Industrial Safety Supply products for your facility. But again, the Industrial Safety Supplies are one piece in an overall injury 'Elimination' Plan. Employeeswont let you down if you are a Leader and approach in an open and honest way.
I wont say Good Luck. Kinda like Gary Player, who once said "the harder I work, the luckier I get"
So work hard at it, and you will no doubt get results.
More Information on Industrial Safety Supplies and where to how to begin a Injury Prevention Plan.